What Is Plastic Injection Molding
Plastic injection molding is a widely employed manufacturing technique for producing plastic components of varying sizes, from small to large. This process involves an injection molding machine, raw plastic material, and a mold. The plastic is first heated until molten in the machine and then injected into the mold, where it cools and solidifies into the final part.
Plastic parts are integral to numerous industries, including automotive, medical, small engine, plumbing, industrial, and agricultural sectors. Leveraging advanced plastic injection molding technologies and processes, manufacturers can achieve exceptional precision and efficiency in producing high-quality plastic components.
The Advantages of Plastic Injection Molding
Plastic injection molding offers several advantages that make it an ideal choice for manufacturing a wide range of parts and products, including silicone keypads. Key benefits include:
Speed and Cost-Effectiveness: The injection molding process is highly efficient and easily automated, resulting in reduced production times and cost savings. This efficiency not only speeds up production but also enhances profitability.
Lightweight: Plastic parts are significantly lighter than metal or steel counterparts. This property makes plastic an attractive alternative for metal-to-plastic conversions, benefiting industries looking to reduce weight and cost.
Superior Quality: Injection molding produces parts with exceptional precision and uniformity. This method ensures high dimensional consistency, supported by advanced practices such as SolidWorks for design validation, RJG eDart process controls, and automation technologies. This is particularly valuable for producing high-quality silicone keypads and other precision components.
Design Compatibility: The process integrates seamlessly with computer-aided design (CAD), computer-aided manufacturing (CAM), and SolidWorks. This compatibility allows for the production of both simple and complex parts, including detailed silicone keypads, while meeting stringent specifications.
Customizable Colors: A wide range of colorants is available, enabling the production of silicone keypads and other components in virtually any color or visual effect.
Customizable Product Traits: Over 15,000 plastic variations are available, allowing customization for specific functional requirements. Additives such as glass fibers for strength or UV protectants for durability can be included, enhancing the performance of silicone keypads and other products.
Compliance: Resins are available to meet various regulatory standards, including FDA, NSF, REACH, and RoHS, ensuring that silicone keypads and other products comply with industry regulations.
Sustainability: The precision and efficiency of injection molding result in minimal waste. Excess material can often be recycled, contributing to environmentally friendly manufacturing practices.
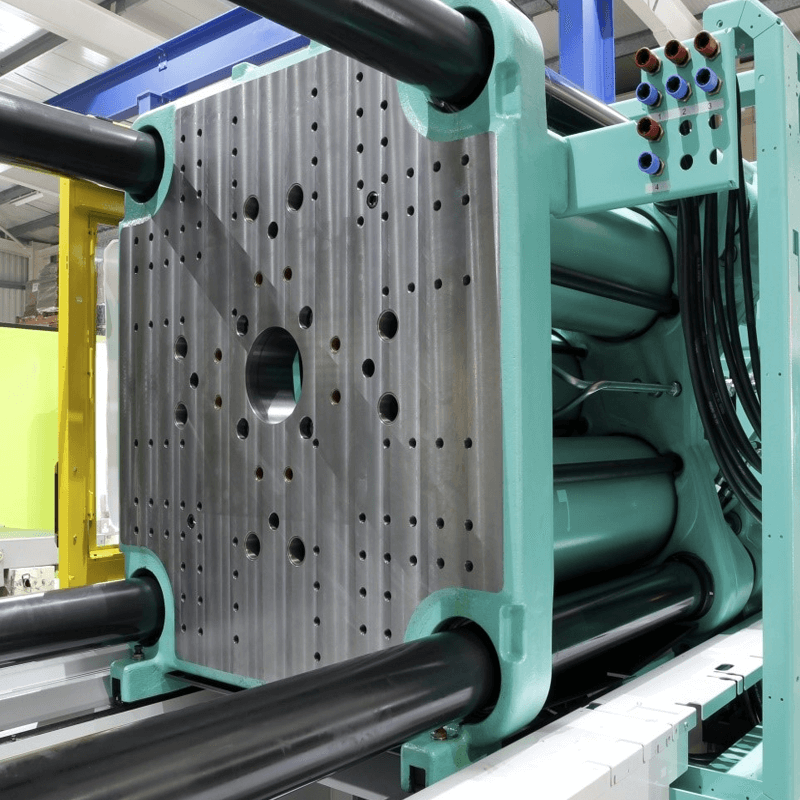
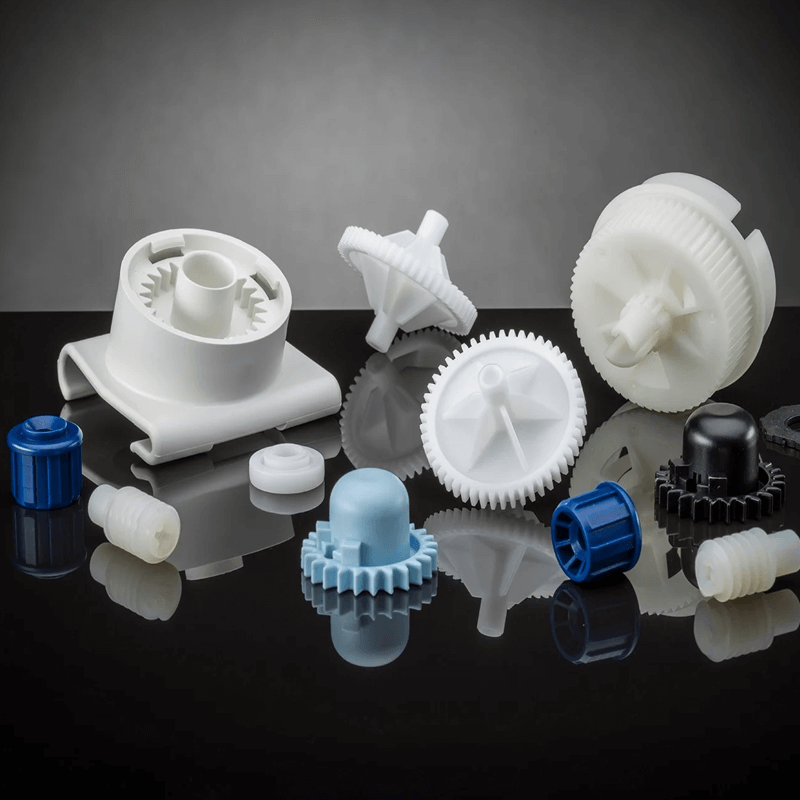
Why Choose Flykeyboard for Plastic Injection Molding
At Flykeyboard, we understand that high-quality production mold tools begin with top-grade raw materials, stringent process controls, and skilled toolmakers. With years of experience, we guarantee repeatable, precise results for your production tooling needs. Here’s why Flykeyboard stands out in high-volume plastic injection molding and tooling services:
Comprehensive Service Offerings
We provide more than just toolmaking and molding. Our all-encompassing service package includes every step of the manufacturing process, delivering a complete solution for your product development needs, including sophisticated silicone keypad production.
Intelligent Project Quotations
We support your development objectives with no minimum order volumes or values for our injection molding services. Our proprietary AI-driven quoting system ensures fast, accurate, and transparent pricing for every project, every time.
Positive Material Identification
Regulatory compliance and peace of mind are guaranteed with our industry-leading positive material identification system. Trust Flykeyboard for precision and reliability in every component, including silicone keypads, where quality must be assured.
Design Optimization
Every project benefits from our comprehensive design-for-manufacturing review. This process enhances the design and production of silicone keypads and other components, ensuring superior results while optimizing time and cost efficiency.
Plastic Injection Molding Tolerances
In plastic injection molding, resins can expand and contract due to temperature fluctuations, mechanical stress, and moisture. Our manufacturing tolerance guide provides essential information on the shrinkage characteristics of various resin types, aiding in your design decisions.
During our design analysis, we identify potential issues such as thermal stress, shrinkage, warping, or other defects that could impact your injection molded parts. For detailed guidance, refer to our manufacturing design guide, which addresses common defects and strategies for their prevention.
Unless specified otherwise, we adhere to the DIN 16742 standard tolerances for injection moldings. Upholding the highest quality standards is a critical aspect of our production process. For further details, consult our visual quality standards guide applied to injection molded components.
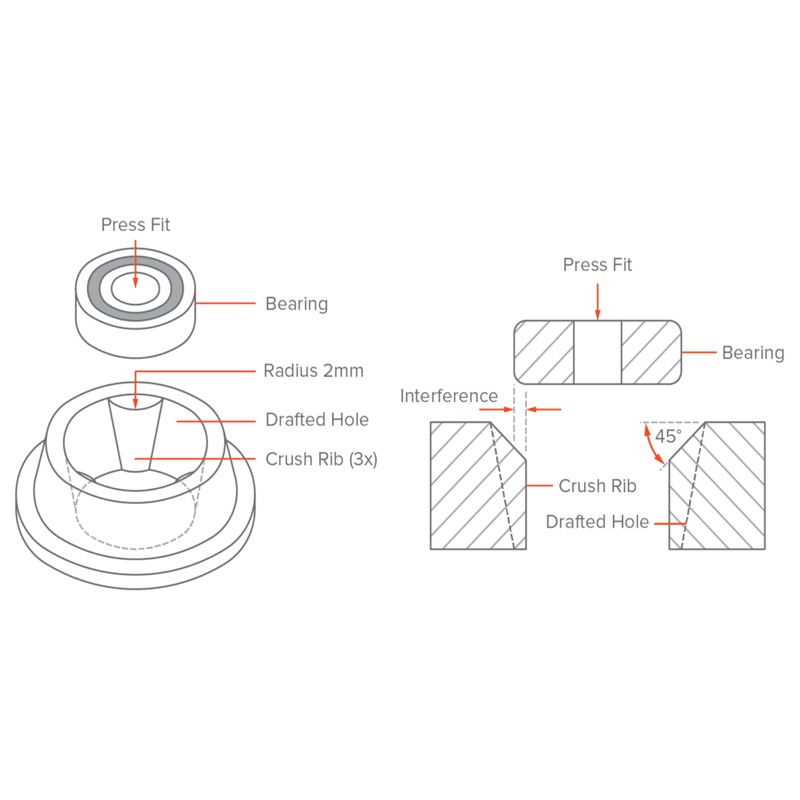
Steps for Developing a Plastic Part
The process of creating custom plastic parts has become increasingly streamlined and accessible. By partnering with an experienced plastic injection molder, you can efficiently develop a well-defined plan, optimize your design, and produce precision parts that accelerate your product’s market entry and adhere to your budget. Here are the key steps in the plastic part development process:
1. Designing the Part
- Develop a detailed design based on functional and aesthetic requirements. This phase involves creating technical drawings and specifications that will guide the mold creation and production processes.
2. Determining the Molding Process
- Select the most suitable molding technique, such as injection molding, based on the part's design, material requirements, and production volume. This step ensures that the manufacturing process aligns with your project’s goals.
3. Prototyping
- Create prototypes to validate the design and functionality of the plastic part. Prototyping helps in identifying any design flaws and making necessary adjustments before proceeding to full-scale production.
4. Manufacturing
- Proceed with the production of the final plastic parts using the selected molding process. This phase involves the actual molding of the part, quality control checks, and final adjustments to ensure the parts meet the desired specifications.
Each step is crucial to achieving a high-quality, precise plastic part. Detailed attention to each phase ensures that the final product meets all design and performance criteria.
Applications of Plastic Injection Molding
Medical Industry
Plastic injection molding is a cornerstone in the medical field, offering a range of benefits such as lightweight properties, non-toxicity, and cost-effectiveness. Key applications include syringes, catheters, dispensers, tubing, and various medical devices. For an in-depth exploration of how plastic injection molding supports medical innovations, visit our blog post.
Consumer Products
Plastic is integral to daily life, found in items we use for both work and leisure. From computer keyboards and mice to game controllers, headphones, toys, and kitchen appliances, plastic injection molding enables the production of a wide array of consumer products. Discover more about the diverse uses of plastic in consumer goods.
Electronics Industry
In the electronics sector, plastic injection molding provides robust, lightweight, and non-corrosive housings for components such as circuit boards, switches, wires, batteries, and sensors. This molding technique ensures protection and user safety while maintaining the integrity of electronic components. Learn how plastic injection molding meets the demanding needs of the electronics industry.
Agriculture Industry
Durability and resistance to UV light and chemicals are essential for agricultural products. Engineered plastic components are utilized in various applications including conveyor belts, drive trains, feeders, water sprinklers, and fencing. Explore why plastic injection molding is an optimal solution for the agriculture sector.