About Silicone Rubber Die Cutting
Die cutting is a specialized shearing technique that utilizes a precision tool, known as a die, to cut through rubber materials with accuracy. The resulting die-cut rubber components can be produced in a variety of shapes, depending on the die's configuration.
This process is particularly advantageous for manufacturing silicone keypads and other rubber products, as rubber is highly amenable to die cutting. Additionally, all rubber compounds can be efficiently processed in mechanized die-cutting systems, which not only accelerate production but also minimize material waste, ensuring cost-effective and sustainable manufacturing
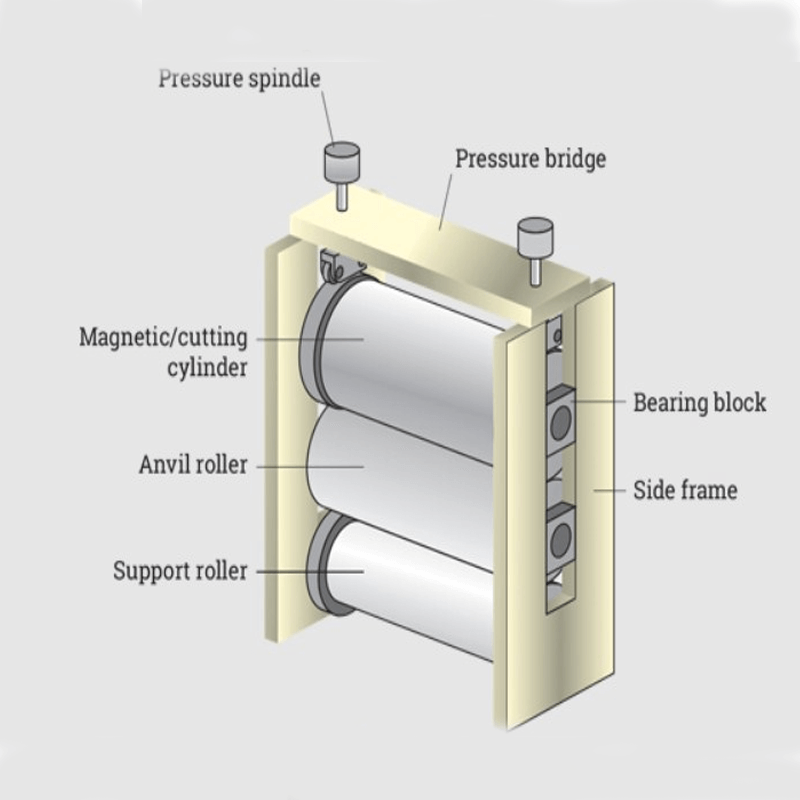
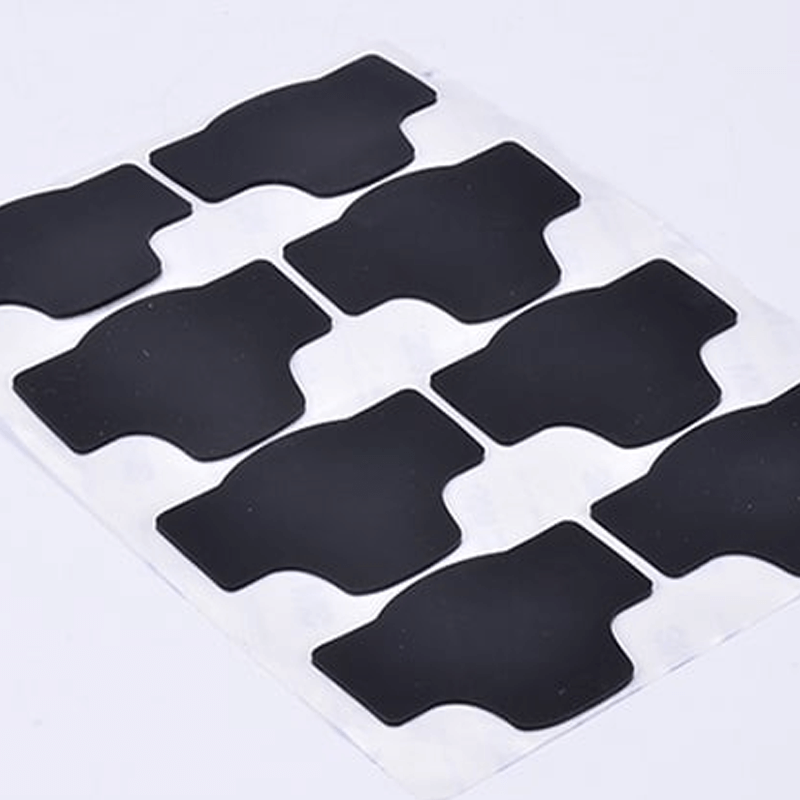
Advantages of Precision Die Cutting
Precision die cutting is a versatile and efficient method for producing complex rubber components. Its ability to achieve high accuracy makes it ideal for manufacturing silicone keyboard components, gaskets, seals, washers, and other intricate parts. This technique is particularly advantageous for projects that require specific materials, designs, and quantities that traditional manufacturing methods struggle to achieve.
With tolerances as tight as ±0.003 inches (0.076 mm), precision die cutting offers superior accuracy compared to conventional machining and stamping processes. This enhanced precision ensures a better fit, reduces material waste, and ultimately saves both time and money in production.
Silicone Die Cutting Process
Design Preparation
The first step in Silicone Die Cutting involves creating precise designs using advanced design software. Computer-aided design (CAD) plays a crucial role in ensuring accuracy. It's important to use high-resolution drawings, preferably at 300 dpi or higher, to guarantee clarity and precision.
Material Selection
Selecting the right silicone material is key to achieving optimal results. High-grade silicone with Shore A values between 30 and 70 is ideal for die-cutting. Additionally, it’s recommended to use silicone sheets that are less than 25 millimeters thick for better performance.
Die Selection
Choosing the appropriate die is essential for the process. Rotary dies are excellent for continuous cutting, while steel rule dies are ideal for more intricate shapes. Rotary dies can have a diameter of up to 16 inches, allowing for versatile cutting options.
Machine Setup
Proper machine setup is critical to the success of the die-cutting process. The machine should be calibrated to match the specific properties of the silicone material. Key factors include adjusting the pressure, ensuring correct alignment, and confirming that the blades are sharp. Precise calibration is essential for achieving clean cuts, especially when working with silicone keypads.
Cutting Process
Silicone sheets are pressed against the dies during the cutting process with carefully controlled pressure. The pressure typically ranges from 25 to 75 tons, depending on the thickness and density of the material. Ensuring the correct pressure is applied is crucial for producing clean, precise cuts without damaging the material.
Extraction
Once the cutting is complete, the parts are carefully extracted from the die. For smaller or more delicate components, tweezers are used to avoid damage. It's important to keep the work area clean and free from silicone debris and dust to maintain quality.
Inspection
Each cut part undergoes a thorough inspection to ensure it meets quality standards. Magnifying glasses or other inspection tools are used to check for defects, such as rough edges or unwanted holes. Parts that do not meet the required standards are rejected.
Packaging
The final step involves packaging the die-cut silicone parts. They are packed in clean, moisture-resistant bags, with silica gel packets added to maintain dryness. The packed parts are then neatly stacked in boxes and placed on pallets, ready for shipment. This ensures that the silicone keypads and other components arrive in perfect condition.
Key Considerations for Cutting Silicone Rubber Keypads
Material Selection
When working with silicone rubber keypads, the material’s softness can lead to concave edges due to deformation during the cutting process. Depending on the application, this effect may be undesirable and should be carefully considered.
Material Density
High-density silicone rubber is stronger and more resilient but also more challenging to cut. Conversely, lower-density silicone is easier to shape and stretch. The choice of material density should align with the specific requirements of the keypad's application.
Material Thickness
Material thickness significantly impacts cutting feasibility. While increased thickness generally enhances the strength of the silicone rubber keypad, it can also render the material unsuitable for die-cutting. Beyond a certain thickness, alternative cutting methods, such as waterjet cutting, may be necessary.
Geometry Design
Die-cutting silicone rubber keypads has a minimum thickness limit of 2.5mm (0.1 inches). For materials thinner than this, waterjet cutting is preferable. Additionally, it's important to account for slight compression in the final product and allow a tolerance of ±0.5mm (0.02 inches) for all dimensions.
Cutting Tolerances
Softer silicone materials typically require more relaxed cutting tolerances compared to rigid materials like sheet metal. For applications requiring tighter tolerances, a solid steel tool or waterjet cutting is recommended over steel rule cutting.
Production Volume
Higher production volumes can significantly reduce the cost per part, making large-scale manufacturing more cost-effective for silicone rubber keypads.
Essential Tools for Die Cutting
Rotary Dies
Rotary dies are integral to the silicone die-cutting process, featuring cylindrical configurations that enable high-speed production. These tools are particularly effective for processing thicker materials, offering cutting depths up to 1.5 mm, thereby enhancing productivity and efficiency in high-volume operations.
Flatbed Dies
For applications requiring precision, flatbed dies are the ideal choice. Commonly utilized in cutting silicone rubber, these dies provide exceptional accuracy. They accommodate material thicknesses up to 25 mm, making them suitable for a wide range of die-cutting projects.
Steel Rule Dies
When robust performance is needed, steel rule dies stand out. These dies are capable of cutting through multiple layers simultaneously, streamlining the production process. With a cutting height of 23.8 mm, steel rule dies are versatile, handling a diverse array of materials with ease.
Laser Cutting Machines
For complex and intricate designs, laser cutting machines offer unparalleled precision and flexibility. These machines are ideal for a wide variety of applications, delivering detailed cuts with a high degree of accuracy.
Why Choose Flykeyboard for Silicone Rubber Die Cutting?
At Flykeyboard, our cutting-edge facility and seasoned professionals deliver top-tier silicone rubber products to clients worldwide. Leveraging our advanced rubber die cutting technology, we are committed to ensuring that you receive the highest quality products tailored to your specific needs.
- Round-the-Clock Expert Support: Our industry-leading experts are available 24/7 to assist you.
- Quick and Accurate Quotes: Receive fast, precise quotations to kickstart your project.
- Custom Designs and Rapid Prototyping: We offer bespoke designs and rapid prototyping to meet your unique requirements.
- Continuous Production: Our facility operates 24 hours a day, ensuring your projects are completed on time.
- ISO 9001:2015 Certified: We adhere to the highest quality standards in the industry.
- Competitive Pricing and On-Time Delivery: Benefit from our best-in-class pricing without compromising on timely delivery.
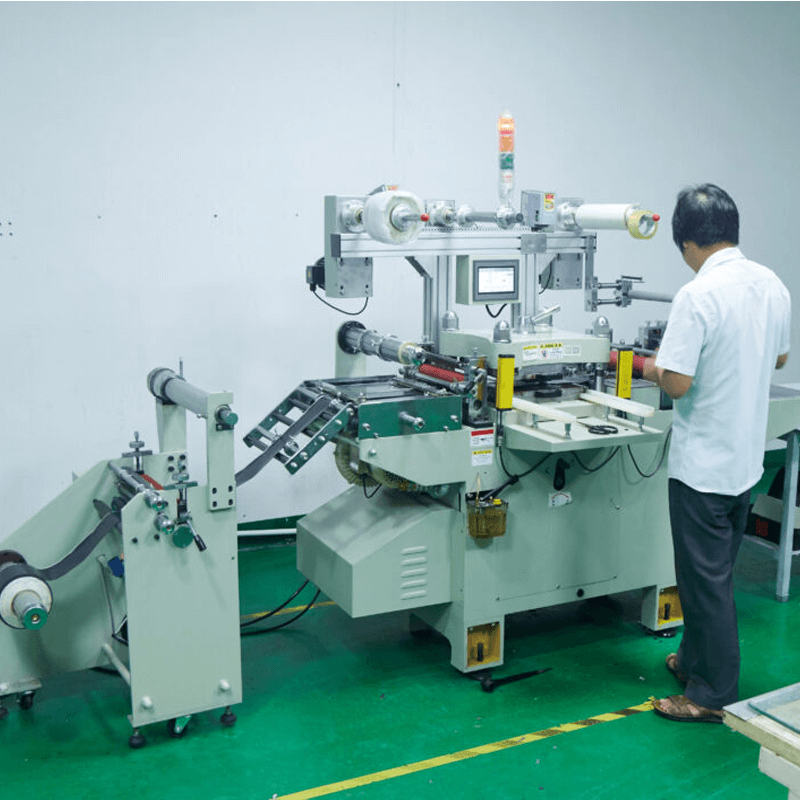
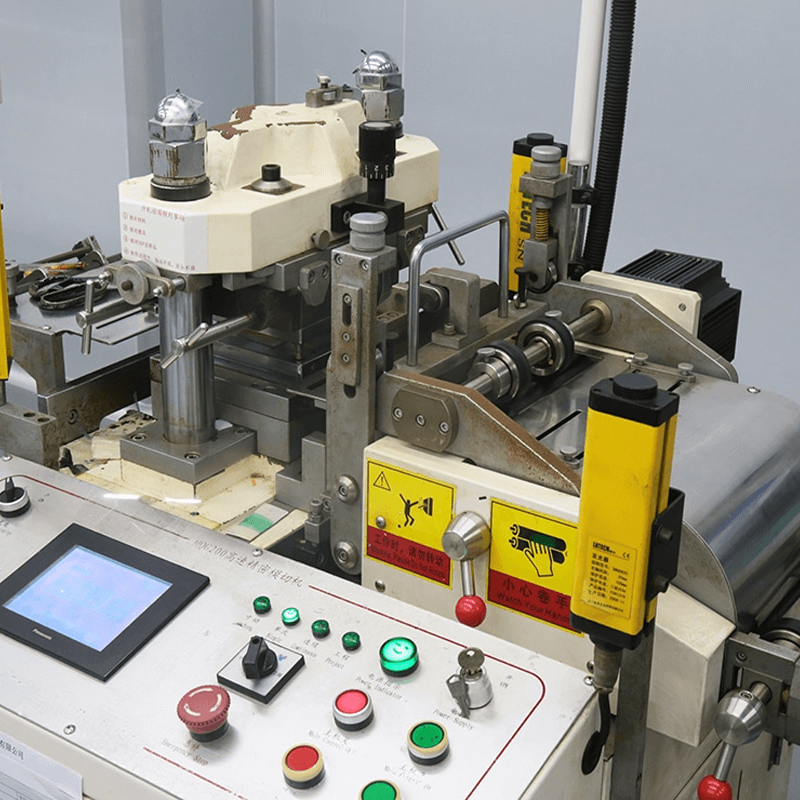
Common Applications of Silicone Rubber Die Cutting
1. Gaskets and Seals: Used in automotive and industrial applications to create precise, durable seals that resist extreme temperatures and chemicals.
2. Keypads: Essential for creating durable and responsive silicone rubber keypads used in electronics, medical devices, and industrial equipment.
3. Insulation: Applied in electronics for thermal and electrical insulation, ensuring safety and performance.
4.Medical Devices: Custom die-cut silicone components are vital in medical devices like seals and tubing, offering flexibility and biocompatibility.